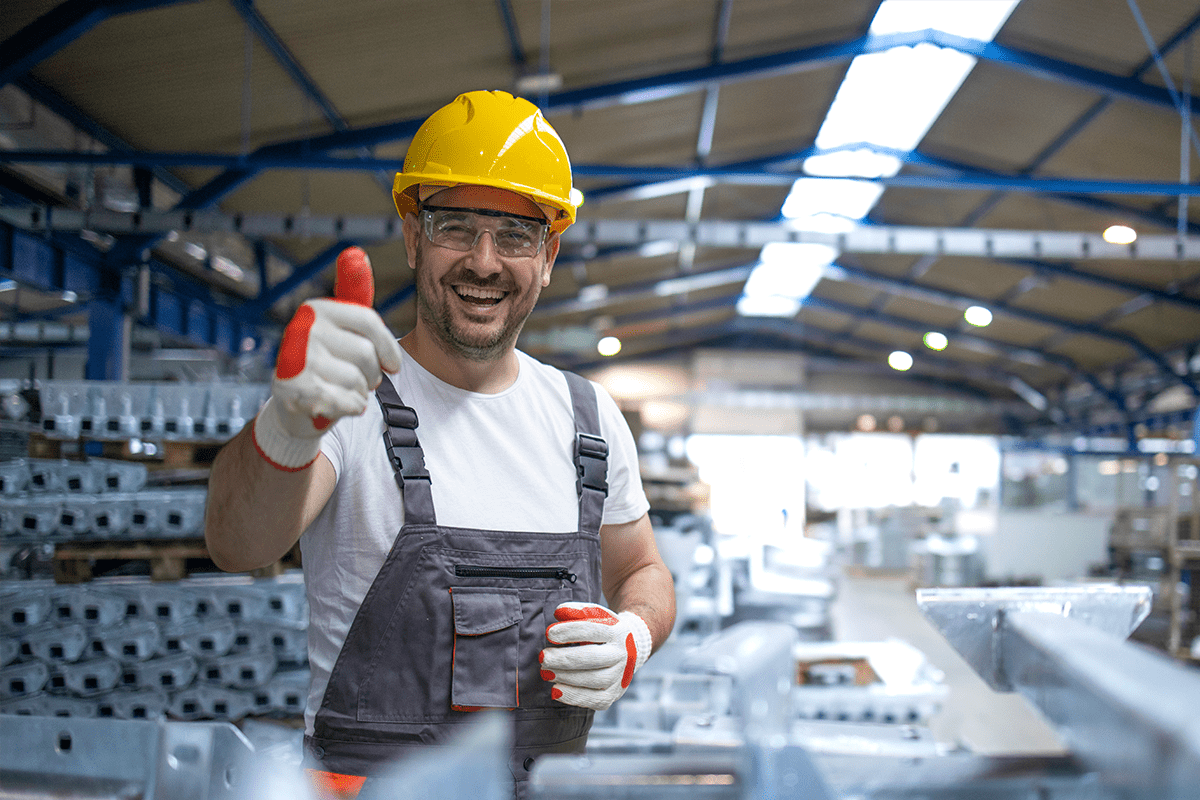
- How can U.S. manufacturers improve workplace safety?
- How does OrthoLive help manufacturers increase employee safety?
The U.S. Centers for Disease Control & Prevention (CDC) estimates more than 13 million American workers are at risk each year of nonfatal or even fatal injuries in the manufacturing field. The responsibility for protecting this workforce rests with the owners and managers of these businesses.
While the overall numbers of workplace injuries and deaths have been declining over the past decade, industry leaders agree that more needs to be done. How can manufacturing plants and other organizations in this field reduce their risk by creating a safer workplace?
How Can U.S. Manufacturers Improve Workplace Safety?
American manufacturing firms can increase plant safety by creating internal mechanisms to organize the workspace and the workers within it. There are seven ways to accomplish this goal, including the following:
- Avoiding worker fatigue
- Creating a culture of safety reporting
- Educating the workforce
- Focusing on ergonomics
- Performing regular equipment maintenance
- Understanding OSHA rules
- Wearing safety equipment
Let’s go over some of the details related to each of these actions.
1. Avoiding Worker Fatigue
This is an often overlooked but critically important part of any safety culture. Worker fatigue is recorded as a significant problem in modern industry due to “high-demand jobs, long duty periods, disruption of circadian rhythms, and accumulative sleep debt that are common in many industries.”
While the employer can’t go home with the worker and encourage them to get more sleep, there are on-the-job factors that the company can control. Fatigue risk management can begin with an evaluation of the workforce conditions that lead to fatigue, from repetitive movement, job stress, or even the humidity or noise levels on the job site.
Employers can educate workers on the value of good sleeping habits but they can also allow and even facilitate naps during breaks or provide caffeine to combat fatigue, which studies show improve worker performance.
2. Creating a Culture of Safety Reporting
Workplace culture is the key to mitigating injury risk in manufacturing. Leaders need to consistently convey the right message, which is that “accidents happen as a result of shortcuts.”
Creating a culture where employees understand why they should report their injuries is also important. From your onboarding process to regular safety training, companies must encourage their workforce to keep a keen eye on workplace conditions that may cause injury to them or someone else.
Interested in additional safety resources that can help create a safety culture? Click here to see our available infographics, on-demand, webinars and more.
3. Educating and Training the Workforce
Educating the workforce in spotting hazards and then creating an environment where they feel comfortable reporting on those problems is just job one. Teaching your workforce to communicate the problem may be just as hard. Employees should be trained in describing the hazard with three key metrics: identify the risk, determine what could happen as a result, and pinpoint how the risk was caused.
As an example, say an employee identifies a piece of equipment blocking a walkway. The questions they should be trained to ask and answer could look like this:
- What is the risk? Someone could trip and fall.
- What could happen? A fall can lead to injury.
- What caused the risk? Lockout/tagout rules weren’t followed.
4. Focusing On Ergonomics
One of the more unseen causes of injury is muscular strain and damage-causing repetitive motions. Since one-third of all OSHA-reported events are musculoskeletal in nature, creating an ergonomic safety program can help workers avoid these kinds of injuries.
There are three key parts to any ergonomic program:
- Teaching employees to avoid tasks that are greater than their body can handle
- Training on the proper way to perform tasks to reduce bodily strain
- Providing remedies for repetitive tasks that cause problems over time
Preventing obvious workplace hazards is easier than focusing attention on the quiet tasks that can lead to repetition injuries. Ergonomic injuries may seem small at first, but they can end up costing big money. An ergonomics program can help mitigate safety concerns related to musculoskeletal strain.
5. Performing Regular Equipment Maintenance
Maintaining equipment not only extends the life of your heavy machinery; it protects the life and health of your workforce. The correlation between machine maintenance and safety is so important that overlooking it could make all of the other components of your safety program useless.
There are three types of regular system maintenance:
- Routine or preventative maintenance to head off unexpected repairs
- Corrective maintenance to get equipment up and running
- Predictive maintenance to track the equipment lifecycle
However, we also know that equipment maintenance can also create risk. OSHA’s Lockout/tagout (LOTO) offers us a methodology for instructing workers to disable machines before performing maintenance. It’s an effective way to provide a foundation for regular equipment inspection and maintenance.
6. Understanding OSHA Rules
Keeping up with OSHA regulations can do more than keep your company from receiving a costly compliance fine—it will also keep your workers safer in the long run. Manufacturers should note the rules related to specific safety incidents, such as machine guarding, equipment operation, and conditions that lead to slips, trips, and falls.
Far too often, employers view OSHA as a punitive organization instead of one with the mission of reducing workplace injuries and deaths, which also serves to cut employer costs associated with these incidents. By forming partnerships with state and federal workplace safety organizations, your company can decrease OSHA reportable incidents, which in turn lessen healthcare and workers’ compensation costs.
7. Wearing Safety Equipment
While this is perhaps an obvious requirement in the manufacturing sector, 98% of workers have reported personally observing employees who failed to wear the proper safety equipment while on the job. 70% of workers have reported experiencing hand injuries due to not wearing gloves when the injury happened.
Every manager and employee, from temp workers to supervisors, should be able to recognize safety gear requirements on the job and feel empowered to speak up should they notice something amiss. This can not only save money in unnecessary injury costs but also potentially save lives.
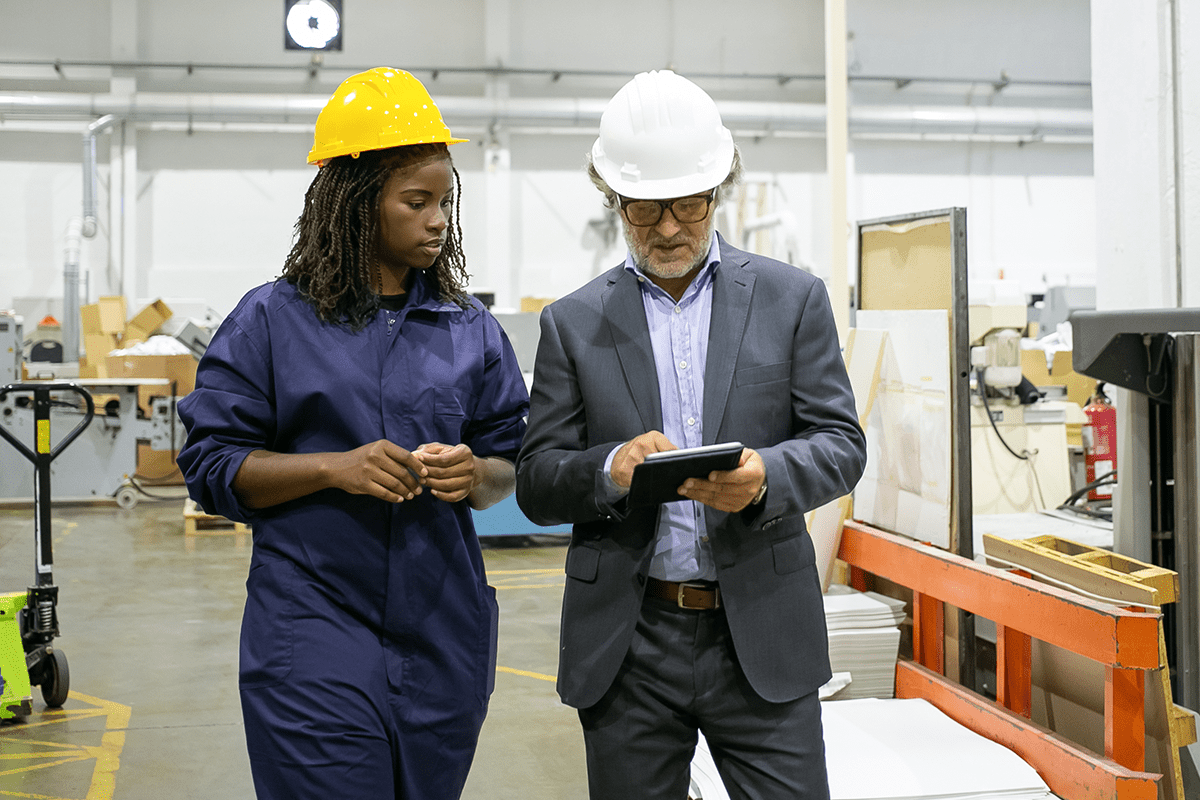
How Does OrthoLive Help Manufacturers Increase Employee Safety?
OrthoLive offers employers 24/7/365 access to licensed injury care experts by phone and video. Our telemedicine platform allows immediate virtual triage of injured employees, allowing your team’s fast medical advice and support.
These programs have shown to reduce the costs of workplace injury claims by up to 80% by eliminating unnecessary trips to the ER while providing the medical care your employees need to get back to work. This more than pays for access to some of the leading injury care providers in the country.
Learn more about how our Remote Injury Care platform can help your manufacturing team stay safer on the job by clicking here.